Vehicle Simulation Laboratory
Facilities
Motion System
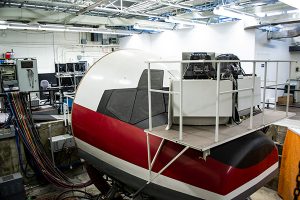
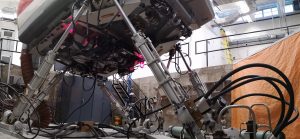
CAE 300 Series Motion System: is a 6 DOF Stewart platform. The actuators have 91.4 cm stroke, 8.9 cm bore, and hydrostatic bearings. Three 37.3kW induction motors with matching variable displacement pumps power the system. The nominal bandwidth is 10Hz (3dB) in gain, or 5 Hz in phase (90 deg phase). VSL has extended the bandwidth to over 15Hz (phase and gain). The motion envelope for the system is:
DoF | Displacement | Velocity | Acceleration |
---|---|---|---|
Surge | +0.7m, -0.61m | 0.7m/s | 1.2g |
Sway | +0.59m, -0.59m | 0.7m/s | 1.2g |
Heave | +0.56m, -0.49m | 0.6m/s | +2g,-0g |
Roll | +21deg, -21deg | 30deg/s | 400deg/s2 |
Pitch | +22deg, -20deg | 30deg/s | 400deg/s2 |
Yaw | +24deg,-24deg | 30deg/s | 400deg/s2 |
Visual System
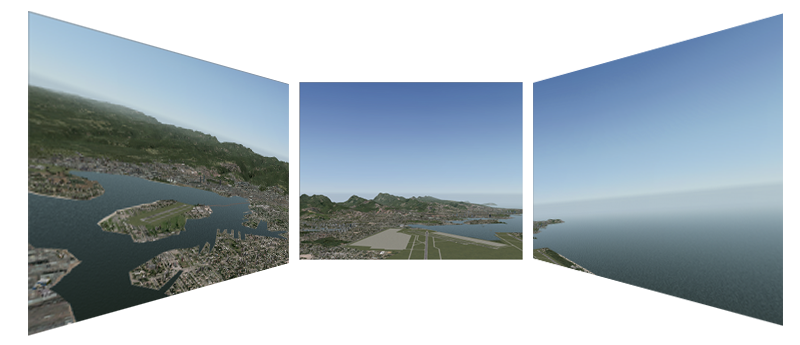
4 Channels nVidia GTX-285, rending with X-plane, 38ms transport delay, 60Hz update. Front cockpit uses 3 Sony monitors projecting through infinity optics boxes. Rear cockpit uses helmet mounted display.
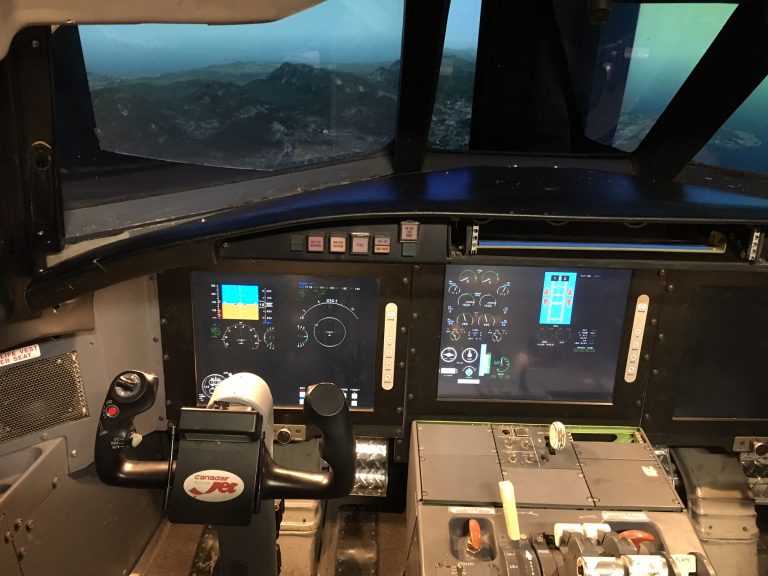
Front Cockpit
Rear Cockpit
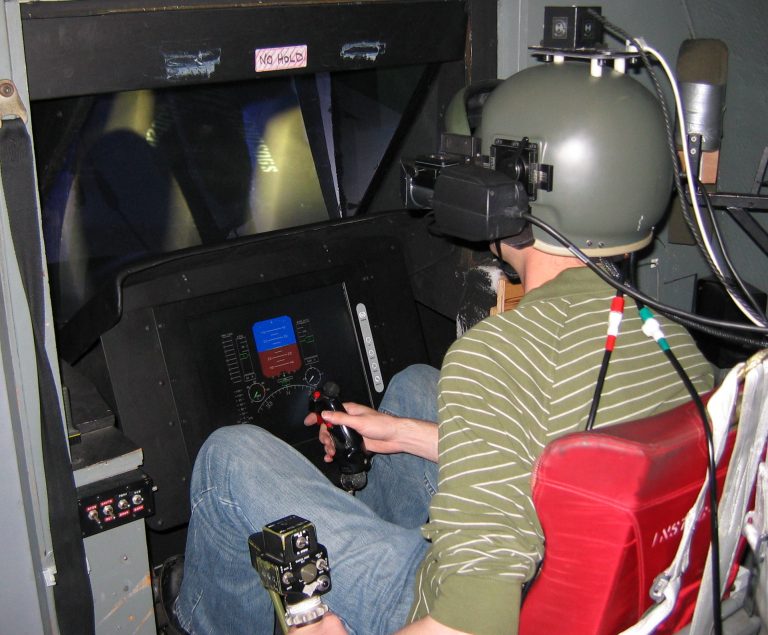
Real Time Host
Operator's Workstation
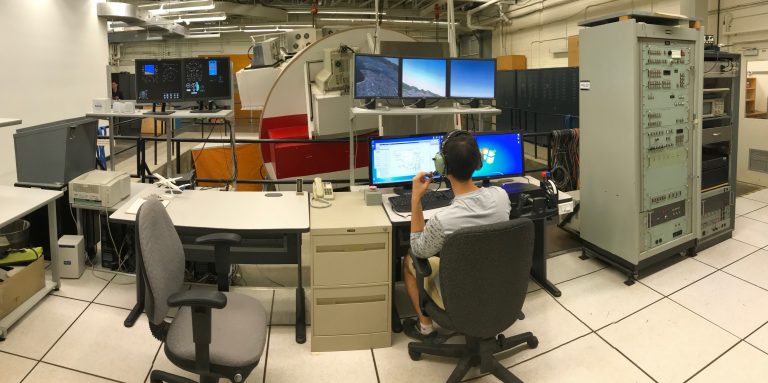